Research into the basics of CNC
The main method of part programme creation is G-code, this is the most widely use programming language in the engineering industry.
The machine control unit (MCU) acts as the centre of a CNC system as it is used to perform functions such as:
Reading coded instructions
Decoding these instructions
Putting interpolations into place in order to generate axis motion commands
Receiving signals of position and speed
Data can be transferred to and from the machine by using wired or wireless network connections in many modern machines, other methods of data transferring includes Bluetooth and using standard V24, RS232, or RS485 serial interfaces.
Datum positioning can be done in a number of ways, one of the more common ways which does not require expensive equipment but is still accurate is using a dowel pin. To do this you go to an external edge using shim paper and slowly moving the dowel pin in until the dowel touches the shim on the edge of the material. Once you have done this you take half the diameter of the and use this to set the datum. Another method of datum positioning for centre line setting is probing two outside edges along one axis, taking the coordinates and finding the centre point going half way between them.
The main method of CNC machine programming is G-code, this is the most widely use programming language in the engineering industry. G-code includes different letter address variables which have different meanings, for example and F variable defines the feed rate and O variable is the program name.
Feeds and speeds can be decided by using a feeds and speeds calculator, the variables that decide the feeds and speeds to be used are based on the hardness of material, cut size, type of tip, the overall condition of the machine (how often it is serviced), the life of the tool being used, angle of cut, cross section of chip, finish desired and whether coolant is being used and what type of coolant it is.
The position of the cutting tool is controlled by the MCU which receives and puts out codes, the programme inputs codes to the MCU which is then decoded and used for positioning and speed of the cutting tool.
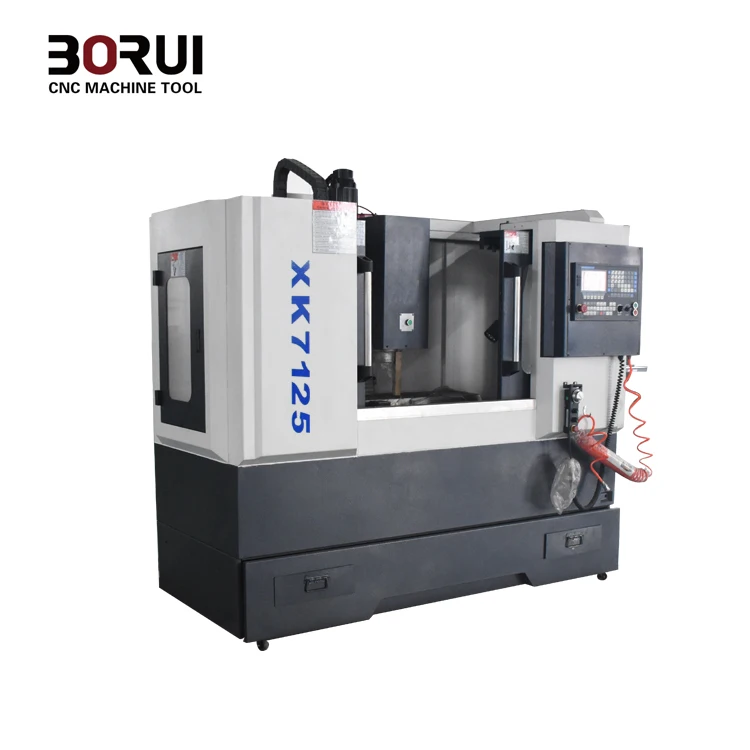 |
3 Axis CNC Milling Station |
Comments
Post a Comment